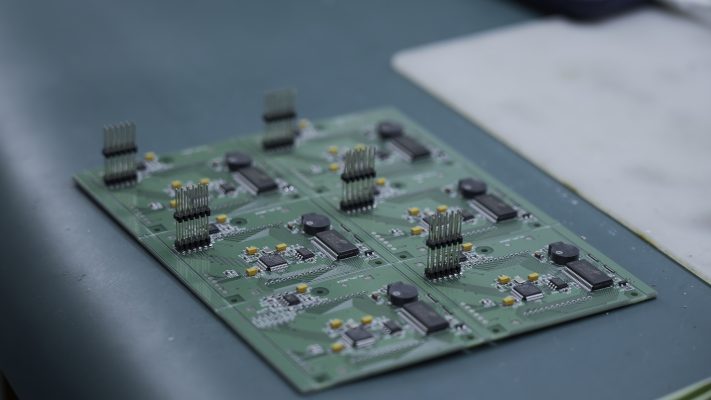
- February 11 2025
In today’s high-speed electronics landscape, signal integrity is paramount. For high-performance systems, ensuring that electrical signals travel cleanly and without distortion is critical. As device frequencies climb and circuit complexities increase, traditional manufacturing methods can no longer guarantee the uncompromised signal quality demanded by modern applications. Advanced PCB manufacturing processes are transforming this scenario, providing the precision and reliability required to maintain superior signal integrity from design through production.
Understanding the Importance of Signal Integrity
Signal integrity refers to the preservation of the quality of electrical signals as they pass through a printed circuit board. In high-speed digital and RF systems, even minor distortions—caused by impedance mismatches, electromagnetic interference (EMI), crosstalk, or thermal effects—can result in data errors or complete system failures. As board designs become denser and operating frequencies rise, maintaining signal integrity is a critical challenge. This makes it essential for manufacturers to implement processes that proactively address these issues.
Challenges in Preserving Signal Quality
Modern PCBs face several inherent challenges that can degrade signal integrity:
• Impedance Discontinuities: Variations in trace width or dielectric thickness can cause impedance mismatches, leading to signal reflections and losses.
• Electromagnetic Interference (EMI): As signal frequencies increase, unwanted electromagnetic emissions can interfere with neighboring circuits, distorting signals.
• Crosstalk: The close proximity of traces in high-density layouts increases the risk of signal coupling between adjacent lines, resulting in interference and data corruption.
• Thermal Effects: Elevated temperatures can alter the electrical properties of PCB materials, further compromising signal quality.
Addressing these issues requires not only sophisticated design techniques but also a manufacturing process that consistently achieves the tight tolerances needed to mitigate these risks.
Advanced Manufacturing Processes: A Technological Shift
Recent advancements in PCB manufacturing processes are pivotal in enhancing signal integrity. These innovations offer the precision and consistency that traditional methods cannot match. Key technological elements include:
• Precision Automation: Automated assembly systems and robotic handling ensure component placement and soldering are executed with micron-level accuracy. This minimizes misalignments and ensures that trace geometries and via placements remain consistent across the board—key factors in maintaining controlled impedance and reducing signal reflections.
• Automated Optical and X-ray Inspection: High-resolution automated optical inspection (AOI) systems, complemented by advanced X-ray imaging, scrutinize every PCB layer for defects. These technologies rapidly identify issues such as solder bridges, voids, or misaligned vias—defects that could impair signal quality. Real-time feedback allows for immediate corrective measures, ensuring that each board adheres to stringent quality standards.
• Real-Time Data Analytics and Machine Learning: Integrated sensor networks across the production line collect continuous data on critical parameters like temperature, humidity, and alignment. By analyzing this data in real time—often with the assistance of machine learning algorithms—manufacturers can detect potential deviations before they impact signal integrity. This proactive approach not only improves yield but also ensures that boards consistently meet performance specifications.
Advanced Routing Techniques and Controlled Impedance
A cornerstone of signal integrity is maintaining controlled impedance throughout the PCB. Advanced manufacturing processes facilitate the precise control required for high-speed designs. With state-of-the-art fabrication techniques, even the narrowest traces and the smallest vias are produced with exacting precision, ensuring that impedance remains uniform.
Additionally, modern design practices such as differential pair routing, where two complementary signals are routed together, help cancel out noise and reduce EMI. Automated systems now routinely implement these techniques, ensuring that trace lengths and spacing are optimized for the best possible electrical performance. The result is a board that not only meets design specifications on paper but also performs reliably under real-world operating conditions.
Material Innovations Supporting Signal Integrity
The choice of substrate and dielectric materials is fundamental to preserving signal integrity. Advances in material science have led to the development of low-loss, high-stability substrates that are ideal for high-frequency applications. These materials help minimize dielectric losses and support consistent impedance across the board.
Leading manufacturing partners, known for their commitment to precision fabrication, have been quick to integrate these advanced materials into their production lines. Their processes ensure that PCBs benefit from improved thermal stability and reduced signal attenuation, which are crucial for sustaining high-speed performance in demanding environments.
Integrating Design and Manufacturing for Optimal Outcomes
Achieving superior signal integrity is not solely about the manufacturing process—it requires a seamless integration between design and production. Modern PCB design tools now incorporate features that account for manufacturing constraints, ensuring that designs are optimized from the outset for both performance and manufacturability. Design-for-manufacturing (DFM) practices ensure that potential issues are identified and resolved early in the development cycle.
By aligning design parameters with advanced manufacturing capabilities, engineers can reduce variability and enhance overall board performance. This integrated approach means that every aspect of the PCB—from trace geometry to material selection—is optimized to support robust signal integrity, even in the most complex and high-speed applications.
Precision Automation: Bridging the Gap Between Innovation and Production
The implementation of precision automation in PCB manufacturing is a game changer for signal integrity. Automated systems not only enhance accuracy but also provide the scalability required for high-volume production without sacrificing quality. In high-end technical manufacturing, where even a few defective boards can have significant ramifications, the reliability offered by precision automation is indispensable.
A notable advantage of these advanced processes is the ability to incorporate real-time adjustments. For instance, during production, automated systems continuously monitor critical metrics. If a deviation is detected, adjustments are made instantaneously—ensuring that the board continues to meet exacting standards. This level of control is especially crucial in high-speed and high-frequency circuits, where even minor variations can lead to significant performance issues.
Thermal Management as a Component of Signal Integrity
Thermal management is intricately linked to signal integrity. As operating frequencies increase, the heat generated by densely packed components can impact both performance and reliability. Advanced manufacturing processes now include integrated thermal management solutions, such as thermal vias and optimized heat sinks, which dissipate heat effectively across the PCB. By maintaining a consistent temperature profile, these measures help preserve the electrical properties of both the substrate and the traces, ensuring that signals remain clear and undistorted.
Looking Ahead: The Future of Signal Integrity in PCB Manufacturing
The evolution of PCB manufacturing is an ongoing journey. Emerging technologies, such as digital twin simulations and additive manufacturing, promise to further enhance signal integrity. Digital twin technology allows manufacturers to simulate the entire production process in a virtual environment, identifying potential issues before they manifest on physical boards. This level of foresight enables continuous refinement of both design and manufacturing processes.
Additive manufacturing, although still in its early stages for PCB production, offers the potential to create complex, multi-layer boards with unprecedented control over material properties and trace geometries. As these technologies mature, they are likely to play an increasingly significant role in ensuring that PCBs not only meet but exceed the performance standards required by high-speed, high-frequency applications.
The integration of IoT principles into manufacturing further enhances the ability to maintain signal integrity. With interconnected sensors and real-time data sharing, every stage of production can be monitored and optimized continuously. This holistic oversight ensures that even the smallest deviation is addressed promptly, preserving the overall quality and performance of the final product.
Bridging Innovation and Performance in Signal Integrity
Enhancing signal integrity in PCB manufacturing is a multifaceted challenge that requires a convergence of innovative design, advanced materials, and cutting-edge production processes. By leveraging precision automation, real-time analytics, and sophisticated inspection technologies, manufacturers are able to produce boards that not only meet but exceed the rigorous demands of modern electronics.
Manufacturers dedicated to high-end technical production are increasingly turning to advanced processes that bridge the gap between design innovation and production excellence. With the support of manufacturing partners who bring unmatched expertise in precision fabrication, companies can achieve the level of quality required for today’s high-speed, high-frequency applications.
In an era where every micron and every degree of temperature matters, the role of advanced PCB manufacturing processes in enhancing signal integrity cannot be overstated. By continuously integrating new technologies and optimizing every aspect of production, the industry is setting new benchmarks for performance and reliability—ensuring that critical electronic systems remain robust in the face of ever-growing challenges.
Elevate Your Signal Integrity with Microchip USA
In a world where every micron and every degree matter, achieving superior signal integrity demands more than just good design—it requires manufacturing excellence. At Microchip USA, our PCB Build Service bridges innovation and performance, delivering precision fabrication supported by ISO 9001, ISO 16949, and UL certifications. With a 10-day average turnaround, competitive pricing, and a relentless focus on quality, we empower you to meet the exacting demands of today’s high-speed, high-frequency applications. Contact us!