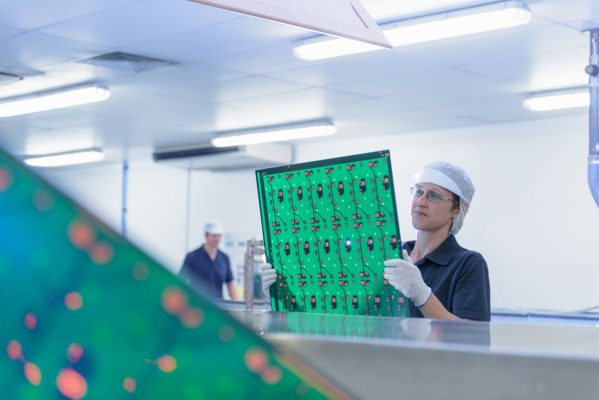
- February 11 2025
Every custom PCB project starts with an innovative idea and culminates in a fully realized product that meets stringent performance and reliability standards. The path from prototype to production can be complex, but with the right strategies and technologies, this journey can be streamlined to deliver high-quality boards quickly and efficiently.
Bridging the Gap Between Concept and Reality
The transformation from a concept to a working prototype is a critical phase in any custom PCB project. Engineers and designers leverage advanced simulation tools and PCB design software to create detailed layouts that capture every nuance of the intended functionality. These digital models are then used to produce initial prototypes, allowing teams to validate designs, test functionality, and identify potential issues early on. By investing in robust design validation, manufacturers can reduce the risk of costly revisions later in the production process.
The Role of Rapid Prototyping
Rapid prototyping has revolutionized the custom PCB journey by compressing the timeline from initial design to physical realization. Techniques such as laser direct imaging (LDI) and high-resolution milling allow for the creation of prototypes with tight tolerances and intricate details. These methods ensure that even the most complex designs are faithfully reproduced, enabling engineers to test boards under real-world conditions. This iterative approach not only accelerates development but also fosters innovation by allowing designers to experiment and refine their ideas quickly.
Advanced Custom PCB Design Tools and Simulation Software
Before a single board is manufactured, advanced design tools play a pivotal role in optimizing the layout for both performance and manufacturability. Simulation software provides insights into critical parameters such as signal integrity, thermal distribution, and power management. This level of analysis ensures that potential issues are identified and addressed during the design phase, paving the way for a smooth transition to production. Incorporating these tools into the workflow minimizes the likelihood of design errors, ultimately saving time and resources in later stages.
Streamlining the Transition to Full-Scale Production
Once a prototype has been rigorously tested and validated, the focus shifts to scaling up production. Transitioning from a single or limited-run prototype to full-scale manufacturing involves a series of carefully coordinated steps. A key element of this process is the refinement of design-for-manufacturing (DFM) practices. DFM principles ensure that the PCB design is optimized for high-volume production by considering factors such as material selection, trace geometry, and layer stack-ups. This proactive approach reduces potential bottlenecks and simplifies the production process.
Precision automation plays a vital role during this phase. Automated assembly systems and robotic handling ensure that every board is produced with consistent quality and minimal human intervention. These systems can handle complex tasks—from precise component placement to meticulous soldering—at speeds far exceeding manual capabilities. The result is a manufacturing process that is both efficient and scalable, capable of meeting the demands of high-end technical applications without compromising on quality.
Embracing Precision Automation in Manufacturing
Automation has emerged as a cornerstone in the modern PCB production environment. By integrating precision robotics and real-time monitoring systems, manufacturers can achieve remarkable consistency across production runs. For example, state-of-the-art automated optical inspection (AOI) systems scrutinize each board layer to identify defects that might compromise performance. These systems work in tandem with automated assembly lines to ensure that every board leaving the production floor meets exacting standards.
A trusted manufacturing partner in the industry leverages such advanced processes to handle complex, custom PCB projects with exceptional accuracy. Their capabilities include not only the use of high-precision robotics but also a suite of inspection technologies that monitor every aspect of the production process. This level of control ensures that the transition from prototype to mass production is smooth and that the resulting products maintain the integrity of the original design.
Rigorous Quality Assurance and Continuous Improvement
Quality assurance is integral to every stage of the PCB journey. After the boards are produced, rigorous testing protocols are employed to verify that each board meets the specified performance and reliability criteria. Automated test equipment (ATE) and in-circuit testing (ICT) systems are used to detect defects and verify electrical performance across numerous parameters. This comprehensive quality control process minimizes the risk of defective boards reaching the customer and helps maintain the reputation of high-end manufacturing operations.
Moreover, continuous improvement is embedded into the manufacturing process through the use of real-time data analytics. Sensors and machine learning algorithms provide insights into production performance, allowing for proactive adjustments and process optimizations. These feedback loops ensure that any deviations are promptly corrected, leading to consistently higher yields and reduced waste. The commitment to quality and continuous improvement is a critical factor in the success of custom PCB projects, ensuring that the final product performs reliably in its intended application.
Custom PCB Collaborative Design and Manufacturing Partnerships
No custom PCB project exists in isolation. Successful projects often result from close collaboration between design teams, manufacturing experts, and technology partners. This collaborative approach ensures that every aspect of the PCB—from the initial design to the final product—is optimized for performance, manufacturability, and cost-effectiveness.
A key advantage of working with an experienced manufacturing partner is their ability to provide design feedback based on real-world production constraints. Their expertise in precision fabrication can lead to design modifications that enhance reliability and performance while streamlining the production process. This iterative dialogue between design and manufacturing teams is critical for addressing potential issues early, ensuring that the transition from prototype to production is as seamless as possible.
Overcoming Production Challenges
The journey from prototype to full-scale production is rarely without challenges. Variations in material quality, fluctuations in production conditions, and the inherent complexity of high-density designs can all pose obstacles. However, by implementing robust process controls and leveraging advanced manufacturing technologies, these challenges can be effectively mitigated.
For instance, precision automation not only enhances production speed but also improves repeatability across batches. Real-time monitoring systems detect even minor deviations in production parameters, allowing for immediate intervention. These measures reduce the incidence of defects and ensure that every board meets the stringent quality standards required in high-end technical manufacturing.
Future Trends in Custom PCB Production
Looking ahead, the evolution of custom PCB production is set to accelerate even further. Emerging technologies such as digital twin simulations are enabling manufacturers to create virtual replicas of production lines, which can be used to predict and optimize performance before physical production begins. This digital approach allows for a level of foresight that significantly reduces the risk of errors during scaling.
Additive manufacturing techniques are also beginning to make inroads into PCB production, offering new possibilities for creating complex, multi-layer boards with enhanced performance characteristics. These advancements, combined with ongoing improvements in automation and quality assurance, promise to further streamline the custom PCB journey from prototype to production.
A Holistic Approach to Custom PCB Excellence
The journey from prototype to production is a critical phase in custom PCB development, requiring a holistic approach that integrates advanced design tools, rapid prototyping techniques, precision automation, and rigorous quality assurance. By embracing each of these elements, manufacturers can not only accelerate the production process but also ensure that the final product meets the highest standards of reliability and performance.
In this evolving landscape, manufacturers that invest in state-of-the-art technologies and foster collaborative partnerships are best positioned to navigate the complexities of modern PCB production. Their commitment to continuous improvement and innovation ensures that every board produced is a testament to precision, quality, and engineering excellence.
From the initial spark of an idea to the full-scale production of high-performance PCBs, streamlining the custom PCB journey is about more than just efficiency—it’s about delivering excellence at every step. By harnessing the latest technological advancements and leveraging the expertise of industry leaders, companies can transform challenging projects into success stories that drive innovation and set new benchmarks in the world of custom electronics manufacturing.
Transform Your Custom PCB Journey with Microchip USA
At Microchip USA, we understand that bringing a custom PCB from concept to production demands more than just speed—it requires a holistic commitment to excellence. With advanced design tools, rapid prototyping, precision automation, and rigorous quality assurance, we deliver high-performance boards that meet the highest standards. Explore our PCB capabilities or contact us today!