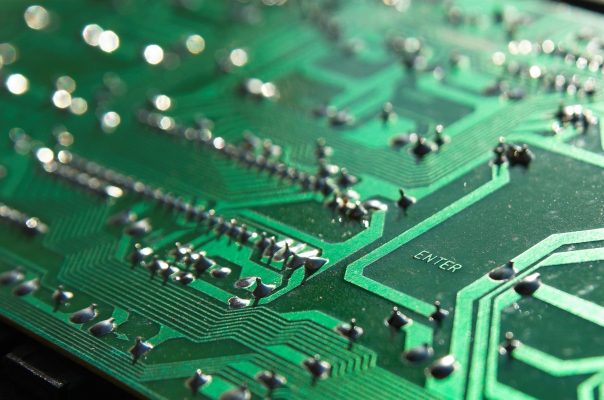
- February 11 2025
In the high-stakes world of advanced electronics manufacturing, the quality and precision of printed circuit boards (PCBs) can determine the success of entire systems. As designs become increasingly complex and performance expectations continue to rise, precision automation in PCB fabrication is emerging as a critical solution. By integrating state-of-the-art robotics, real-time data analytics, and advanced quality control measures, manufacturers are transforming production processes to achieve unmatched quality and efficiency.
The Imperative for Precision in PCB Fabrication
Modern electronic systems demand extraordinary precision. Even the smallest deviation in PCB fabrication can have a cascading effect on system reliability and performance. With tighter tolerances and increasingly complex layouts, the margin for error is minimal. Manual processes—once the backbone of PCB production—are no longer sufficient to meet the stringent requirements of high-end manufacturing. Precision automation minimizes human error and ensures that every board is produced under optimal conditions, meeting the exacting standards necessary for mission-critical applications.
Unpacking Precision Automation
At its essence, precision automation involves the use of highly advanced machinery and software to control every stage of the PCB fabrication process. This integration of technology not only accelerates production but also dramatically enhances quality control. Key components of this revolution include:
- Robotic Handling and Assembly: Robotic systems now execute tasks like component placement and soldering with micron-level accuracy. These machines dynamically adjust to variations, ensuring components are placed correctly and consistently every time.
- Automated Optical Inspection (AOI): AOI systems use high-resolution cameras paired with sophisticated image processing algorithms to detect defects early in the production line. Issues such as solder bridges, misalignments, or insufficient solder paste are flagged almost instantly, enabling rapid corrective actions.
- Real-Time Data Analytics: Modern fabrication lines are equipped with a network of sensors that monitor variables such as temperature, pressure, and alignment in real time. This continuous flow of data allows for immediate adjustments, ensuring that even slight deviations are corrected before they result in defects.
Benefits of Harnessing Precision Automation
The integration of precision automation in PCB fabrication offers a multitude of benefits tailored to the demands of high-end technical manufacturing:
• Superior Quality and Consistency
Automation guarantees that every PCB is manufactured under uniform conditions, reducing variability and ensuring exceptional quality. The elimination of manual error is particularly critical in applications where even a minor defect could lead to significant system failures.
• Increased Production Efficiency
Robotic systems can operate around the clock, significantly cutting down cycle times without sacrificing accuracy. This continuous operation not only boosts production volumes but also allows manufacturers to respond more rapidly to market demands.
• Enhanced Yield and Reduced Waste
By catching defects early, automated systems help to minimize the production of faulty boards. This proactive approach not only improves overall yield but also contributes to more sustainable manufacturing practices by reducing material waste and energy consumption.
• Scalability and Flexibility
Precision automation systems can be scaled to accommodate varying production volumes. Whether shifting to a new design or increasing output, these systems offer the flexibility needed to adapt quickly to changing market conditions without extensive downtime.
Technical Innovations Driving the Revolution
Several groundbreaking technologies are propelling the shift toward automated PCB fabrication:
• Advanced Robotics:
Modern robotic arms, equipped with adaptive sensors and AI-driven controls, are redefining what is possible in PCB assembly. These systems can dynamically compensate for variations in component size or placement, ensuring flawless execution even in the most intricate designs.
• Machine Learning in Quality Control:
Machine learning algorithms analyze historical and real-time production data to predict potential defects before they occur. This continuous learning process enables systems to fine-tune their performance over time, resulting in consistently high-quality outputs.
• High-Density Interconnect (HDI) Technologies:
As PCBs evolve to accommodate denser circuit configurations, traditional manufacturing methods struggle to maintain the necessary precision. Precision automation facilitates the creation of HDI boards by ensuring that even the most tightly packed circuits are produced with impeccable accuracy.
• Integration of IoT and Industry 4.0:
The emergence of the Internet of Things (IoT) in manufacturing has led to interconnected production lines where every component communicates seamlessly. This holistic integration enables manufacturers to monitor, analyze, and optimize every aspect of the production process, from raw material handling to final quality checks.
Overcoming Challenges in the Transition to Automation
Despite its clear benefits, transitioning to a fully automated fabrication process is not without challenges. High initial capital investment, the requirement for specialized technical expertise, and the complexities of integrating new systems with legacy equipment are common hurdles. However, these challenges are increasingly viewed as necessary investments toward achieving long-term gains in quality and efficiency.
A successful transition begins with a detailed assessment of current production capabilities. Manufacturers must identify bottlenecks and areas where automation can yield the highest returns. Collaborating with technology partners who specialize in high-end manufacturing solutions can also streamline the integration process. With careful planning and a commitment to continuous improvement, the return on investment becomes evident through reduced operational costs, higher yields, and enhanced competitiveness in the global market.
Future Outlook: A New Era of High-Performance PCB Manufacturing
Looking ahead, the role of precision automation in PCB manufacturing is set to expand further. As industries such as aerospace, medical imaging, and telecommunications continue to push the boundaries of technology, the demand for ever more reliable and high-performance PCBs will only grow. Emerging trends such as quantum computing, advanced materials science, and digital twin technology promise to revolutionize how production processes are simulated and optimized before implementation on the factory floor.
In this evolving landscape, manufacturers that invest in the latest automation technologies will be better positioned to adapt to rapid technological advancements. The ability to quickly integrate new innovations into existing processes is critical for maintaining a competitive edge. Moreover, as environmental concerns become increasingly important, the efficiency gains from precision automation—such as reduced material waste and lower energy consumption—will contribute significantly to sustainable manufacturing practices.
Final Thoughts
Precision automation in PCB fabrication is more than just an upgrade in technology—it represents a fundamental shift in how high-end electronic components are produced. The benefits of automation, from superior quality and consistency to enhanced production efficiency and scalability, are critical for meeting the demands of modern, high-performance applications. As advanced robotics, machine learning, and IoT integration continue to evolve, the future of PCB manufacturing promises even greater levels of innovation and reliability.
For manufacturers dedicated to producing cutting-edge electronics, embracing precision automation is not merely an option; it is an imperative. By investing in these technologies today, companies are setting the stage for a future where quality is uncompromised, production is seamless, and every PCB contributes to the success of the next generation of electronic systems. The journey toward fully automated, precision-driven fabrication is well underway, and its impact will be felt across the entire spectrum of high-end technical manufacturing.
Take the Next Step with Us
At Microchip USA, we’re leading the charge toward a new era in PCB manufacturing. Our PCB Build Service offers a revolutionary combination of cutting-edge capabilities, ISO 9001, ISO 16949, and UL certifications, and a 10-day average turnaround—ensuring you receive the precision, reliability, and speed your projects demand. All at competitive pricing. Ready to transform your production with the next generation of PCB technology? Contact us!