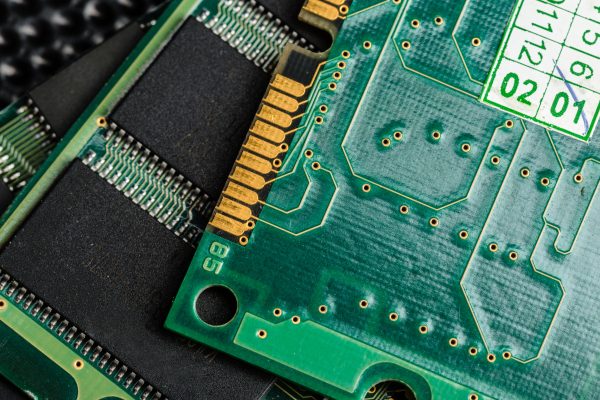
- February 11 2025
In today’s landscape of advanced electronics, the push for smaller, more powerful devices is driving an increased reliance on high-density printed circuit boards (PCBs). These boards, with their intricate layouts and closely packed components, are the backbone of systems where failure is not an option. Maximizing reliability in such designs requires a multifaceted approach that combines innovative design techniques, state-of-the-art manufacturing processes, and strategic material choices. By leveraging cutting-edge technology and partnering with a leader in precision fabrication, manufacturers can overcome the inherent challenges of high-density PCB design to deliver boards that consistently perform under demanding conditions.
The Imperative for Reliability in High-Density Designs
High-density PCBs are engineered to support the ever-growing performance and miniaturization requirements of modern electronic systems. The density of these boards means that any small flaw can lead to critical issues such as signal degradation, thermal overload, or even complete system failure. Ensuring reliability in these environments is paramount. When components are packed tightly together, even minute variations in manufacturing can result in significant performance losses or reduce the lifespan of the board. For high-performance applications where consistency and durability are essential, manufacturers must employ rigorous design and fabrication methodologies to minimize risk and enhance reliability.
Challenges in High-Density PCB Design
Designing PCBs with high-density layouts presents a unique set of challenges that require innovative solutions. One of the primary hurdles is managing signal integrity. With traces often in close proximity, there is a higher risk of crosstalk and electromagnetic interference (EMI), which can compromise the performance of the board. Additionally, the tight spacing increases the likelihood of thermal hotspots, where excessive heat can lead to material degradation or component failure.
Another challenge lies in the complexity of the routing and layering process. High-density designs often necessitate multiple layers and the use of microvias or blind and buried vias to create the necessary interconnections. This complexity not only makes the design process more demanding but also places increased pressure on the manufacturing process to maintain precision and alignment across layers.
Innovative Design Techniques for High-Density Boards
Addressing the challenges of high-density PCB design begins at the drawing board. Engineers are now utilizing advanced design software and simulation tools to model and predict potential issues before a board goes into production. Techniques such as signal integrity simulation, thermal analysis, and electromagnetic modeling help identify and mitigate risks early in the design phase.
One notable strategy is the use of high-density interconnect (HDI) technology. HDI techniques allow for finer traces and smaller vias, which enable more complex and compact designs without sacrificing performance. Additionally, designers are increasingly employing differential pair routing and controlled impedance traces to combat issues of signal loss and crosstalk. By integrating these design practices, engineers can create PCBs that not only meet the rigorous demands of high-density applications but also push the boundaries of what is achievable in modern electronics.
Integrating Advanced Manufacturing Processes
The journey from design to a reliable, high-density PCB is greatly influenced by the manufacturing process. Advanced fabrication techniques have become essential to meet the stringent tolerances and precision required. A key element in this process is the integration of precision automation. By employing state-of-the-art robotics and automated assembly lines, manufacturers can achieve micron-level accuracy in component placement and soldering—ensuring that each board adheres to exacting specifications.
A leading manufacturing partner in the field is renowned for its ability to produce high-density boards with exceptional consistency. With an emphasis on high-precision fabrication, this partner employs a suite of advanced technologies, including automated optical inspection (AOI) systems that quickly detect defects and real-time data analytics that monitor production variables. This commitment to precision ensures that even the most complex high-density designs are manufactured to the highest standards, greatly enhancing overall reliability.
Embracing Precision Automation and Real-Time Analytics
Precision automation is revolutionizing the way high-density PCBs are fabricated. Automated systems can maintain consistent quality across large production volumes, reducing the variability that often plagues manual processes. Real-time analytics further augment this approach by providing continuous feedback on critical parameters such as temperature, alignment, and material stress. These insights enable rapid corrective actions during production, effectively preempting potential defects.
This advanced level of control and monitoring is particularly beneficial for high-density designs, where even the slightest deviation can have significant repercussions. The integration of machine learning algorithms into these systems allows them to learn from historical production data, continuously refining their performance. As a result, manufacturers can not only boost production efficiency but also achieve remarkable improvements in board reliability and performance.
Strategic Material Selection and Thermal Management
The choice of materials plays a pivotal role in the reliability of high-density PCBs. Manufacturers are increasingly turning to advanced substrates and dielectric materials that offer superior thermal conductivity and stability. These materials are critical in managing the heat generated by densely packed components, preventing thermal hotspots that could otherwise lead to premature failure.
In tandem with material innovations, thermal management techniques are being refined to address the unique challenges of high-density designs. Incorporating features such as thermal vias, heat sinks, and advanced cooling solutions helps dissipate heat more effectively, thereby maintaining the integrity of the board over extended periods of operation. By combining strategic material selection with innovative thermal management practices, manufacturers can significantly enhance the durability and reliability of high-density PCBs.
Leveraging Leading Manufacturing Expertise
Maximizing the reliability of high-density PCB designs is not solely about innovative design and advanced materials—it also hinges on the capabilities of the manufacturing process. One of the most critical elements in this ecosystem is partnering with a fabrication provider known for its expertise in handling complex, high-density projects. This partner’s commitment to quality is evident in their use of cutting-edge production techniques, precision automation, and stringent quality control measures.
Their advanced fabrication capabilities enable them to manage the intricate details required by high-density layouts, from the precise formation of microvias to the alignment of multiple layers. The combination of these advanced processes ensures that every board meets the rigorous demands of high-performance applications. Moreover, the continuous investment in next-generation manufacturing technologies positions them as a trusted partner for those seeking to push the limits of PCB reliability.
Future Trends in High-Density PCB Design
Looking forward, the field of high-density PCB design is set to benefit from ongoing advancements in both design and manufacturing technologies. Emerging trends, such as the integration of digital twin technology, promise to further streamline the design-to-production cycle by enabling virtual testing and optimization before physical fabrication begins. Additionally, the evolution of additive manufacturing techniques could offer new avenues for creating complex, multi-material boards that enhance performance while reducing production times.
As the demands of modern electronics continue to evolve, the importance of reliable high-density PCB design will only grow. Manufacturers who adopt these cutting-edge approaches, supported by robust partnerships and advanced automation, will be well-positioned to meet the challenges of tomorrow’s technology landscape. Through a combination of innovative design techniques, strategic material choices, and precise manufacturing processes, the future of high-density PCB design is one marked by enhanced reliability and sustained performance.
In an environment where every micron and every degree of temperature counts, the convergence of advanced design practices and state-of-the-art manufacturing creates a pathway to exceptional reliability. By continuously pushing the boundaries of what is possible, the industry is not only meeting current challenges but also setting the stage for the next wave of technological innovation.
Shape the Future of High-Density PCB Design with Microchip USA
As high-density PCB technology evolves, success depends on turning cutting-edge trends into real-world performance. At Microchip USA, our PCB Build Service is engineered to help you do exactly that—offering precision manufacturing, ISO 9001, ISO 16949, and UL certifications, competitive pricing, and a 10-day average turnaround. Whether you’re exploring digital twin integration, additive manufacturing, or next-generation materials, we provide the speed, quality, and expertise you need to bring complex, high-reliability designs to life. Contact Us!