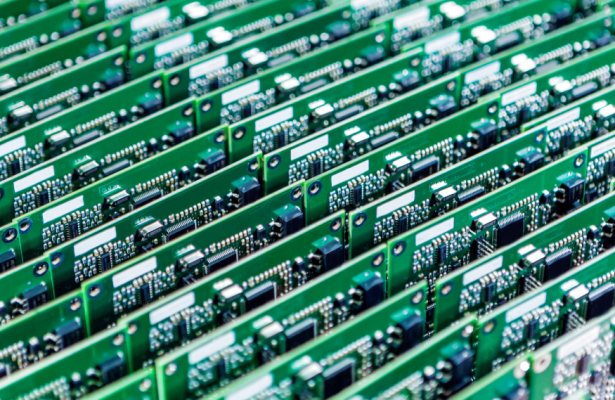
- June 24 2025
Every electronics engineer faces a fundamental choice early in the design process: single-layer or multi-layer PCBs? This decision isn’t just about stacking conductive layers; it shapes cost, performance, manufacturability, and even the lifespan of the final product.
The debate between single-layer and multi-layer PCBs mirrors a broader engineering truth: simplicity and complexity each have their place. A single-layer board, with its straightforward construction, is like a well-designed manual tool, reliable, cost-effective, and easy to fix. A multi-layer PCB, on the other hand, is more like precision machinery, capable of handling intricate tasks but requiring greater expertise and investment.
To effectively compare single-layer and multi-layer PCBs, we must look beyond layer count and examine their real-world implications. Where does one excel over the other? When does the added complexity of multiple layers justify the cost? And in an era of shrinking, high-speed electronics, is single-layer technology still relevant?
This article will explore these questions with the clarity engineers need and the strategic depth that defines great design decisions. Let’s begin with the basics.
What Defines Single-Layer and Multi-Layer PCBs?
At their core, printed circuit boards exist to connect components electrically while providing mechanical support. But how they accomplish this varies dramatically between single-layer and multi-layer designs.
Single-Layer PCBs
A single-layer PCB consists of just one conductive copper layer laminated onto an insulating substrate, typically fiberglass (FR-4). Components mount on one side, while a flat network of traces occupies the opposite side. This straightforward approach has powered everything from vintage radios to modern LED lights.
Multi-Layer PCBs
When engineers need more real estate without expanding the board’s footprint, they turn to multi-layer PCBs. These sandwich multiple conductive layers between insulating dielectric material, connected vertically through plated holes called vias. A modern smartphone motherboard might pack 10 or more layers into a space no larger than a credit card.
The distinction goes deeper than layer count. Single-layer boards follow a linear design philosophy where every connection must exist on one plane. Multi-layer designs embrace three-dimensional thinking, allowing:
- Dedicated power and ground planes for cleaner power delivery
- Shielded signal layers to prevent interference
- High-density interconnects for complex circuits
This fundamental architectural difference leads to divergent applications. While a garage door opener might use a single-layer board, the control module in an electric vehicle demands multiple layers to handle power distribution, sensor inputs, and communication buses simultaneously.
As we examine their pros and cons, remember: the best PCB choice isn’t about technological superiority, it’s about matching the solution to the problem at hand. The next section will explore exactly where each type excels and where it falls short.
Performance and Design Considerations
The choice between single-layer and multi-layer PCBs fundamentally alters how a circuit performs in real-world conditions. Let’s examine the critical factors that differentiate these architectures.
Signal Integrity Challenges
Single-layer designs face inherent limitations in high-frequency applications. Without dedicated ground planes, return paths become unpredictable, leading to electromagnetic interference issues. Multi-layer boards solve this through controlled impedance routing between reference planes, making them indispensable for modern high-speed digital circuits.
Thermal Management Realities
Heat dissipation follows radically different paths in each design. Single-layer PCBs rely entirely on surface area for cooling, while multi-layer variants can:
- Use internal copper layers as heat spreaders
- Incorporate thermal vias to conduct heat away from hotspots
- Implement buried copper regions for localized cooling
Power Distribution Networks
The difference in power delivery highlights why complex systems demand multiple layers. Single-layer boards struggle with voltage drop across long traces, forcing designers to oversize conductors. Multi-layer designs dedicate entire layers to power distribution, providing low-impedance paths that maintain stable voltages across the board.
Physical Constraints and Routing Density
Modern components like BGA packages with 0.4mm pitch simply can’t be reasonably routed on single-layer boards. The escape routing requirements alone force the use of multiple layers. However, for through-hole components with generous pitch, single-layer remains not just viable but optimal from a cost perspective.
Manufacturing Yield Factors
Each additional layer introduces new failure modes in production:
- Layer-to-layer registration tolerances
- Via plating quality
- Interlayer contamination risks
Single-layer boards avoid these complexities entirely, resulting in higher yields for simple designs.
The decision matrix becomes clear when examining actual use cases. Industrial control systems often use 2-layer boards as a sweet spot between cost and capability, while RF front-end modules might require 6+ layers to maintain signal purity. The next section will quantify these differences through real-world performance benchmarks.
Cost Analysis and Production Realities
The financial implications of PCB layer count extend far beyond raw material costs, creating complex trade-offs between upfront expenses and long-term value.
Fabrication Economics
Single-layer PCBs represent the most cost-effective entry point, with production costs typically 60-80% lower than comparable 4-layer boards. This stems from:
- Fewer processing steps (no lamination or via plating)
- Higher pcb fabrication yields (>99% for simple designs)
- Reduced material consumption
Multi-layer boards introduce exponential cost growth – each additional layer increases price by 30-50% due to:
- Additional copper and prepreg materials
- More complex drilling and plating processes
- Increased inspection requirements
Hidden Cost Factors
While single-layer designs win on unit price, they often lose on total system cost in complex applications:
- Larger board sizes may be needed to accommodate routing
- External shielding components add BOM expenses
- Rework costs increase due to layout limitations
Prototyping vs. Mass Production
The break even point varies dramatically by volume:
- <100 units: Single-layer often remains cheaper even with size penalties
- 100-1,000 units: 2-layer becomes competitive
- >1,000 units: Multi-layer optimizations justify upfront costs
Lifecycle Considerations
Enterprise buyers must evaluate:
- Design reuse potential (multi-layer offers more headroom)
- Technology migration paths (DDR5 requires 6+ layers)
- End-of-life costs (simpler boards have higher recyclability)
The cost conversation ultimately hinges on whether you’re building a disposable gadget or a platform meant for evolution.
Innovation Frontiers: Pushing the Limits of Both Technologies

The PCB industry continues to evolve, with both single-layer and multi-layer technologies undergoing significant advancements that are redefining their traditional roles. Modern pcb manufacturing innovations are transforming what was once considered possible with basic single-layer boards. Cutting-edge subtractive-additive hybrid processes now enable 50μm traces on single-layer designs, performance that previously required multi-layer construction. Engineers are also implementing embedded component technology, printing passive components directly onto substrates, while advanced materials like polyimide-based substrates allow single-layer boards to withstand higher operating temperatures without requiring complex lamination.
At the other end of the spectrum, multi-layer technology is experiencing its own revolution. The development of any-layer HDI has eliminated traditional via stacking constraints, while emerging 3D printed electronics enable truly three-dimensional conductive structures that challenge conventional PCB design paradigms. Perhaps most remarkably, optical interconnects are beginning to replace copper traces in certain high-speed applications, representing a fundamental shift in how we think about board-level connectivity.
Perhaps most interesting are the innovations blurring the lines between these two approaches. Semi-additive processes now create quasi-multi-layer functionality on single-layer substrates, while localized multi-layer sections can be incorporated into predominantly single-layer boards. The emergence of programmable conductive inks that can modify routing post-manufacture suggests a future where the distinction between single and multi-layer becomes increasingly fluid. A compelling example of this convergence can be seen in Tesla’s latest battery management systems, which strategically combine single-layer flexible PCBs with multi-layer “islands” only where absolutely necessary, achieving 40% cost savings compared to conventional approaches while maintaining performance.
These developments point toward a fundamental shift in PCB design philosophy. We’re moving beyond simple layer-count considerations into a more nuanced era where engineers can select and combine technologies to precisely meet their specific requirements. The question is no longer simply “single or multi-layer,” but rather how to strategically leverage the full spectrum of available technologies to create optimized solutions. This evolution promises to give designers unprecedented flexibility but also requires a deeper understanding of the expanding range of options at their disposal.
The Future of PCB Design: Beyond Layer Count
The evolution of PCB technology is moving toward a more nuanced design philosophy — one where layer count becomes just one variable in a broader engineering equation. Rather than treating single-layer and multi-layer as binary choices, forward-thinking designers now approach board architecture as a spectrum of possibilities, each with its own advantages for specific applications.
Material Innovations Redefine Possibilities
Advanced substrates are transforming what both single-layer and multi-layer boards can achieve. High-frequency laminates with ultra-low dielectric loss enable single-layer RF designs that previously required multiple layers. Meanwhile, thermally conductive dielectrics in multi-layer boards solve heat dissipation challenges without bulky external solutions. The emergence of nano-engineered materials suggests a future where the very distinction between conductive and insulating layers may blur, enabling entirely new circuit architectures.
Manufacturing Flexibility Unlocks New Designs
Digital printing technologies are revolutionizing PCB production, allowing for hybrid approaches that combine the best of both worlds. We now see boards where certain areas employ complex multi-layer routing while others maintain single-layer simplicity — all on the same substrate. This localized complexity approach, exemplified by Tesla’s battery systems, demonstrates how strategic layer deployment can optimize both cost and performance.
The Rise of Application-Specific Architectures
Increasingly, the most innovative designs don’t conform to traditional layer-count categories. Foldable electronics use single-layer flex circuits in ways that achieve multi-layer functionality through mechanical design. 3D-printed electronics create conductive structures that defy conventional layer stacking altogether. Even conventional rigid boards now often incorporate embedded passive components, reducing the need for additional layers while improving performance.
A New Design Paradigm Emerges
The future belongs to engineers who view layer count not as a constraint but as a flexible design parameter. The most successful designs will likely combine:
- Single-layer simplicity where possible
- Targeted multi-layer complexity where needed
- Emerging technologies like printed electronics where advantageous
This evolution demands a more sophisticated approach to PCB design, one that considers not just electrical requirements but also thermal, mechanical, and even lifecycle factors. The boards of tomorrow won’t be judged by how many layers they have, but by how intelligently they use whatever layers they need.
When sourcing PCBs for your next project, Microchip USA supports a wide range of technologies with our PCB manufacturing solutions. Whether you need standard or multi-layer PCBs, large format, ultra-thin, high-density interconnect PCBs, we’re here to meet the diverse needs of modern electronics. We utilize cutting-edge manufacturing processes and strict quality control while delivering fast turnaround times for our customers. Contact us today!