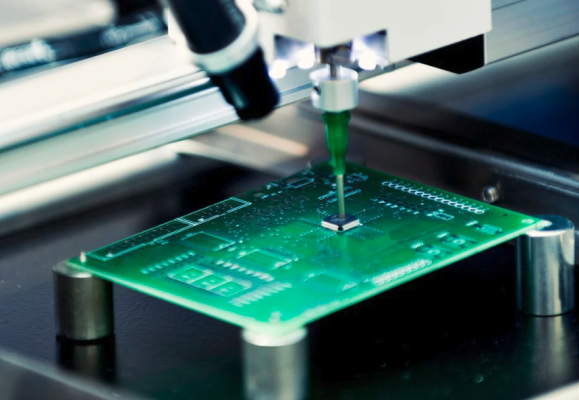
- July 2 2025
The era of predictable PCB lead times is over.
Gone are the days when you could plug layer count and complexity into a simple formula and get a reliable fabrication timeline. What was once a linear equation: layers + features = days, is now a fluid negotiation with geopolitics, material shortages, and even AI-driven factory scheduling.
The Death of the Fixed Timeline
Manufacturers have stopped promising firm delivery windows because production time “depends on complexity, layers, and quantity.” This disclaimer reflects a fractured supply chain where material availability changes weekly. This isn’t temporary volatility. It’s the new normal.
In the past, lead time was a scheduling concern. Today, it’s a design constraint, as critical as trace width or thermal performance. Consider that a 4-layer board with in-stock FR4 might ship in 10 days, while that same design with Rogers 4350B could take 20+ days, and a last-minute DFM rejection could add another week
The difference between best- and worst-case scenarios now spans weeks, not days. For hardware teams, this variability introduces two existential risks:
- Missed market windows (when competitors ship first)
- Cost explosions (when rush fees chew through budgets)
The New Playbook
Smart teams are adapting their workflows. First, by designing for availability and starting with materials checks before schematic capture. If your fab’s Rogers inventory is low, can you use Isola instead? Next, staggered prototyping by ordering test coupons for high-risk materials first and validating before committing to full production. Finally, supplier transparency is required. That means treating lead times as live data.
The Coming Disruption
The PCB industry is ripe for its “AWS moment.” Why? Because AI-driven DFM could slash respin delays, digital inventory can enable real-time lead time quotes, and on-demand regional fabs may emerge to bypass ocean freight. The winners won’t be those who lament volatility, but those who bake it into their design DNA.
The Hidden Costs of Expedited PCB Turns
Expedited manufacturing services present a dangerous illusion. When fabricators advertise “5-day quick-turn” options, they’re not offering true efficiency; they’re monetizing desperation. The economics of rushed production rarely justify the premium. Paying 300% more to halve your lead time might make sense on paper, but the hidden trade-offs create cascading risks.
Compressed timelines eliminate flexibility when you need it most. Once a rush order enters production, even minor design tweaks become impossible. More critically, the same accelerated schedule that delivers boards faster also squeezes quality assurance windows. Fabricators maintain profitability on quick-turn orders by reducing inspection rigor, which is a dangerous compromise that can surface as field failures.
The reality contradicts the marketing. Most expedited services simply prioritize your order in the queue rather than fundamentally accelerating the manufacturing process. Material shortages still delay shipments. Design issues still trigger respins. The premium you pay buys queue position, not actual process improvements.
Strategic teams deploy quick-turn services surgically. For prototype iterations where learning velocity outweighs cost, the premium makes sense. For production batches where reliability and per-unit cost matter more than schedule, conventional timelines prove smarter. The wisest engineers maintain relationships with multiple fabricators, allowing them to route rush orders to shops with verified quick-turn capacity rather than paying premiums for hypothetical acceleration.
This landscape demands new evaluation criteria. Instead of asking “Can we get it faster?”, leading teams now ask:
- What design compromises does this acceleration require?
- Which validation steps will get compressed?
- How does the cost premium compare to program risk?
The most sophisticated organizations have stopped viewing expedited turns as emergencies, instead budgeting for them as calculated program risks, with contingency plans that make rushed production the exception rather than the norm.
The 5 Design Choices That Inflate Your Lead Time
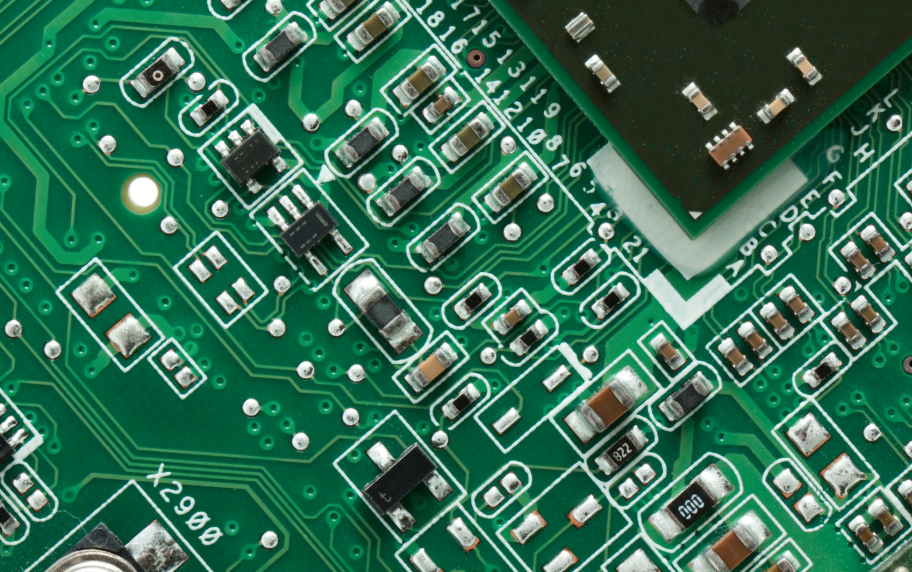
Most engineers blame suppliers when PCBs arrive late. But the truth is harder to swallow: your PCB design decisions are often the bottleneck.
The Material Mismatch
Specifying Rogers 4350B when your fab’s inventory shows Isola FR408 in stock isn’t just a cost problem, it’s a scheduling one. Every specialty material request triggers a supply chain scavenger hunt. The lead time difference between in-stock and special-order substrates can exceed two weeks.
Overengineering the Stackup
That 12-layer board with mixed dielectric constants might be technically elegant, but it’s a manufacturing nightmare. Each additional layer and material interface introduces new alignment and lamination challenges. Sometimes, splitting into two simpler 6-layer boards actually delivers faster.
Compare single-layer and multi-layer PCBs
Tighter Tolerances Than You Need
Demanding 5% impedance control when 10% would work isn’t precision, it’s queue positioning. Tighter specs force fabs to use slower, more meticulous processes. Your ±5% board might wait behind fifty ±10% panels in the production schedule.
The Forgotten Silkscreen Tax
That last-minute logo addition or revised component designator? It forces a full artwork re-review. What feels like a five-minute file update can trigger a 48-hour DFM revalidation cycle and forfeit your place in line in the process.
The Prototype-to-Production Lie
Assuming your NPI board will translate directly to mass production is the ultimate lead time killer. The 8-layer prototype that worked perfectly might require a complete redesign for volume manufacturing. Smart teams now design for scalability from day one.
The best designs aren’t just functional, they’re fabrication-aware.
Rethinking PCB Lead Times: A Strategic Approach
The most effective way to reduce PCB lead times isn’t paying for expedited service; it’s designing for manufacturability from the start. While manufacturers rarely guarantee specific timelines, the fact is that simpler designs consistently move faster through fabrication. The key is understanding how every design decision impacts the production queue.
The Lead Time Leverage Points
- Standard materials ship faster than specialty substrates
- Relaxed tolerances avoid precision manufacturing queues
- Panelized designs often complete sooner than large monolithic boards
- Complete, clean design files prevent DFM-related delays
Reducing PCB delivery times requires planning, which means pre-validating designs against your fab’s capabilities and inventory. Teams that succeed don’t just design boards; they design for their chosen manufacturer’s workflow.
The implications are clear. While you can’t control global supply chains, you can control how your designs interact with them. The difference between a 10-day and 20-day lead time often comes down to three strategic choices:
- Selecting materials your fab stocks routinely
- Resisting over-engineering where simpler solutions work
- Building relationships that provide visibility into real production schedules
This approach transforms lead time from a frustrating variable into a manageable design parameter. The best teams aren’t those that wait the shortest, they’re those that design the smartest.
The 3 Documents That Reveal Your True PCB Lead Time
Manufacturers’ lead time estimates can be tough to pin down, but by analyzing three critical files before submission, engineers can predict actual production timelines with remarkable accuracy.
Your stackup specification serves as the first reality check. A simple 4-layer FR4 board might sail through fabrication, while the same layer count mixing Rogers and FR4 materials could encounter delays. The more exotic your material stack, the further you drift from any fab’s “average” timeline.
The second crucial document is your fabricator’s live inventory report. For example, Microchip USA’s “10-day average turnaround” becomes meaningful when cross-referenced with their current material availability. Leading manufacturers now provide real-time stock levels and alternative material matrices, and smart teams consult these before finalizing designs. Finding your specified substrate marked “low stock” often provides the first warning of potential delays.
Finally, your DFM readiness checklist makes the difference between smooth production and frustrating respins. Modern teams maintain checklists covering:
- Fabricator-specific clearance rules
- Impedance modeling requirements
- Annular ring exceptions
- Solder mask technical constraints
These three documents form a powerful lead time prediction system. Your stackup reveals complexity penalties, the inventory report shows material risks, and the DFM checklist prevents avoidable delays. Teams using this approach consistently achieve more reliable timelines than those relying on generic lead time estimates.
The implications are clear: in today’s volatile manufacturing environment, lead time management begins during design, not at order submission. The most successful engineers treat PCB fabrication as a measurable design constraint rather than an unpredictable black box.
The Coming Revolution in PCB Lead Time Management
The PCB industry stands on the brink of a fundamental shift in how lead times are calculated, communicated, and controlled. What was once a frustrating game of estimates and surprises is evolving into a precise engineering parameter thanks to two emerging technologies.
Digital Twins: From Guesswork to Certainty
The concept of a digital twin, a virtual replica of your physical PCB, is transforming lead time prediction. Manufacturers are beginning to implement systems where your design files don’t just go to quote, but actually simulate through the entire production process. This means that virtual queue positioning shows real-time scheduling impacts, material compatibility checks flag potential delays before submission, and process simulations identify manufacturing bottlenecks in advance.
AI-Driven Dynamic Routing
Static estimates based on historical data are still useful. Still, new approaches use artificial intelligence to continuously evaluate capacities, dynamically route orders based on real-time shop floor conditions, and predict and mitigate delays before they occur.
The Strategic Implications
These shifts are fundamentally changing how hardware teams work:
- Design becomes a closed-loop system where manufacturability feedback happens in real-time
- Lead time transforms from a constraint to a variable that can be actively optimized
- Supply chain resilience increases as alternatives are pre-qualified and ready
The PCB lead time challenges of the past decade were merely symptoms of an immature industry. As digital twins and AI mature, we’re entering an era where “How long will this take?” receives the same precise answer as “What’s the dielectric constant?”
The question isn’t whether this future is coming, it’s whether your team will be leading or following when it arrives. And Microchip USA is the perfect partner to fabricate the custom printed circuit boards you need for your next project. As a U.S. based company with extensive international production capabilities and expert DFM feedback, we can guarantee high-quality PCBs at competitive prices. Get a quote today!